How OEE Calculation Can Help in Education of Employees
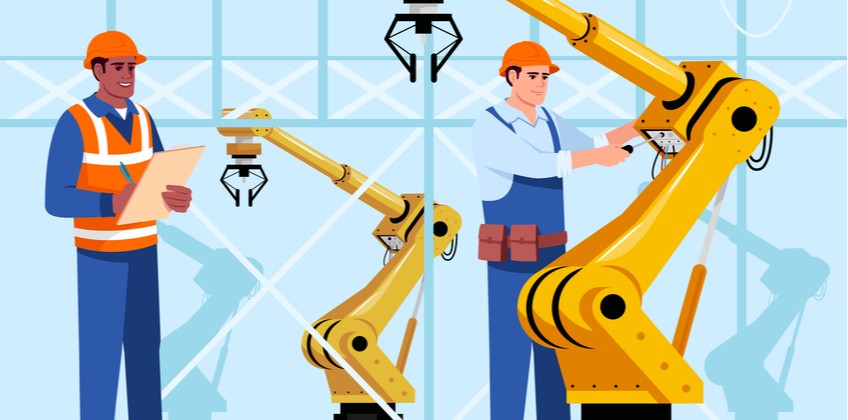
The definition of OEE or Overall Equipment Effectiveness means a standard, which is used to measure manufacturing productivity. Some other simple definition of OEE or Overall Equipment Effectiveness is that the manufacturing time’s percentage is identified through OEE, and that is truly productive. In more simple word, the definition of OEE can also be described in this way, an OEE of 100% means in your production process you are manufacturing good parts, quickly with no stop time. Another definition of OEE is that it is a measurement for production efficiency. OEE comprises of 3 factors i.e. availability, performance and quality.
Calculating OEE –
OEE how to calculate is what people want to know. Therefore, method of OEE calculation is OEE=AxPxQ. i.e. Availability x Performance x Quality. There are some other ways of OEE calculation also. OEE, how to Calculate? Some of the ways of OEE calculation is OEE= (Good count x ideal cycle time)/planned production time. But, if you want to know OEE how to calculate it?. Then one of the common ways of OEE calculation is OEE = Availability × Performance × Quality. There are other complicated ways of calculation also, but you should stick these easy ways of OEE calculator. In the OEE language, it would mean 100% quality, 100% performance, and 100% availability with no stop time.
OEE Calculator –
With the help of OEE calculation formula or calculator, you can perform the best practices for manufacturing. Through the OEE calculation or calculator and by measuring losses in the production process, the manufacturer can broaden their horizons on how to enhance the manufacturing process that too systematically. OEE is the only best metric for identifying losses and benchmark progress and enhancing the production process or productivity of manufacturing equipment by eliminating waste. The preferred OEE calculation or calculator or formula is A x P x Q = OEE. This is one of the best calculators of OEE.
OEE Calculation –
The OEE or Overall Equipment Effectiveness formula calculation is done by multiplying availability, performance, and quality, which is represented by a percentage. In finding out the OEE of an asset or overall asset effectiveness, you will have to start the OEE calculation or calculation or calculator by measuring availability that is calculated by dividing the total run time of an asset with the total planned production time of an asset. An assets level of productivity is measured through overall asset effectiveness, which is maintenance KPI. If you want to know how efficacious an asset is during the manufacturing process, you can get to know it through OEE combination of 3 factors i.e. availability, performance, and quality.
Important Factors –
The important three factors for OEE calculator or formula is asset availability, asset performance and production quality. And, you will note that, through this OEE formula, you can get to know about something different of how an asset operates. When after OEE formula application, if your asset works with an OEE of 100% it would mean that every item it produces is without any kind of defect in quality. One of the best ways OEE formula calculation can be done is to find out the underperforming assets and link poor performance with one or more of the 3 factors of OEE i.e. availability, performance and quality.
Cost Control –
OEE helps mainly in reducing and controlling cost. One of the things, you will know about OEE is that, it is a great metric for identifying the places where you are getting losses. Its main objective is to reduce the cost. What are the types of cost that manufacturer would consider? There are some main types of cost components associated with any process. Two of the main costs are labor cost and cost of materials. OEE helps in making a cost model that will help you to identify and reduce the cost. You can check the OEE index of any manufacturing unit. Most of them update the OEE index every hour. OEE indicators are time, speed and quality. You can check online the speed OEE index, and then quality OEE index, and time OEE index. This way you can use the calculator to calculate the indicators.
Benchmark of OEE –
As per OEE benchmark, 85% of OEE is considered, as world class for manufacturers. Other benchmark of OEE suggests that, 60% of OEE is typical for discrete manufacturer and it shows a substantial room for improvement. In addition, some benchmark of OEE suggests that 100% is perfect in production, manufacturing only good parts. One of the great tools for managers is OEE Overall Equipment Effectiveness. But for plant floor employees, OEE Overall Equipment Effectiveness can be a bit intellectual. When, the plant floor employees are given goals that are online, it is then they perform the best. An OEE benchmark of 40% is very low score.